Case Studies
MUMBAI HOSPITAL
We have created this business case to validate our claim that Transmsonk EC motor technology blended with customised automation based on necessity pays off by reducing energy bills and carbon footprints for hospital chains, hotels, commercial buildings, etc.It has not just helped the end user save energy bills by more than 30% but also removed the challenges faced in the maintenance and operation of the AHU.
SOLAR POWER GENERATION/INVERTER
In the year 2021, it is a well-known fact that we have been recovering from the second wave of COVID, and because of global supply chain issues, most businesses were impacted.There was a rise in power demand and energy bills across the country.In the middle of this situation, one of the global solar plant operating companies contacted us to discuss the issues they are facing with their inverters due to a large number of FAN failures
Successful installation
Our OEM base
Carbon footprints impacted
About Us
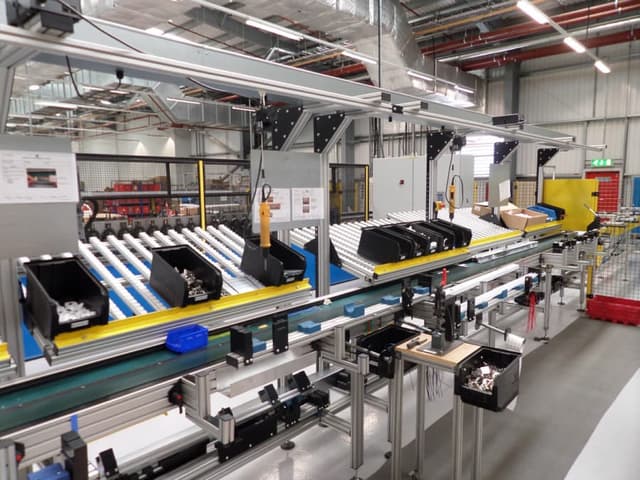
Transmonk India Pvt. Ltd. is into the manufacturing and supply of energy-efficient fans (IE4+ motors), controllers, and automated solutions for different industries.
We are one of the leading electromechanical software companies, backed by highly skilled techno-commercial engineers who have an immense understanding of fans, controllers, and motors. With a strong engineering background, we understand the value of quality products, which assists us in leaving a mark on our OEM customers.
Our focus is to deliver energy efficient and smart solution to our customer.
Currently, we are serving industries and applications like data centres, clean rooms, pharma equipment, commercial buildings, and cold rooms. Further, we are aspiring to expand into industries like poultry, agriculture, smart AHU, and retrofit pace.
See moreFAQ
Electronically Commutated EC Motor. An electronically commutated (EC) motor is designed to run on an alternating current (AC) power supply, but it in fact bears a closer resemblance to a direct current (DC) motor. It is essentially a permanent magnet, brushless DC motor that incorporates on-board electronics. The added electronics allow an EC motor to combine the best features from both AC and DC motors, and then improve on them. For this reason, an EC motor is in a category of its own.
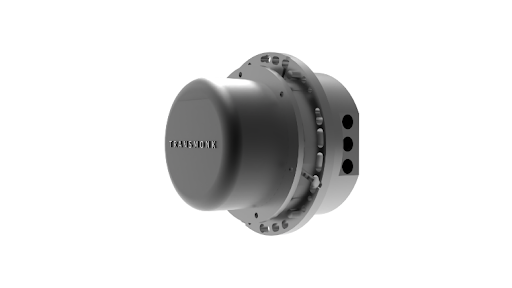
By utilizing this technology, EC fans are highly efficient and pay for themselves through lower operating costs and extended service life. They also provide many operational benefits that are often overlooked. Once these attributes are fully recognized in India ,EC fans will become the next revolution in the air movement industry.
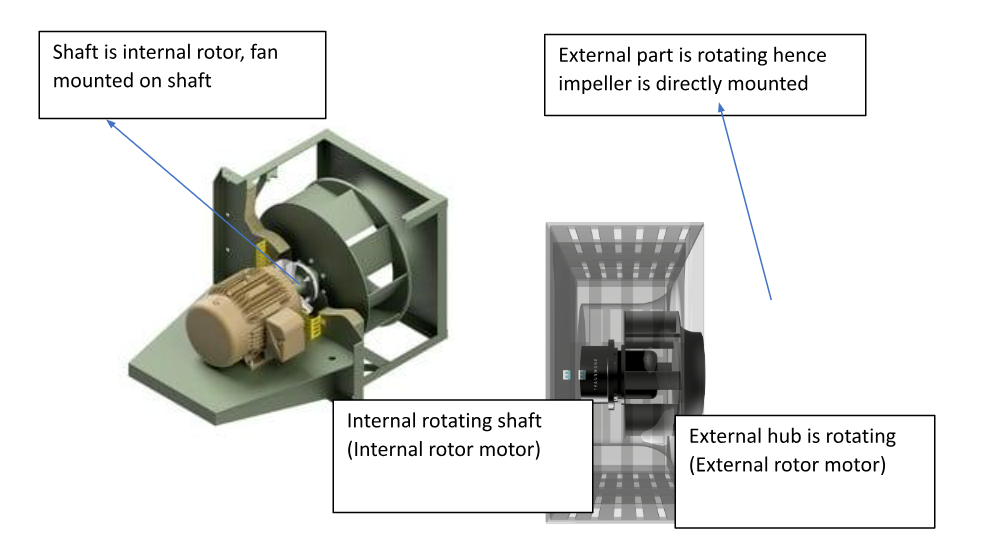
Motors come in a wide range of shapes and sizes, with the conventional style being the internal rotor configuration.
Internal rotor motors are designed with the stator (stationary component) fixed to the motor housing. The rotor (rotating component) is located inside the stator and transmits torque through the output shaft. A fan impeller is typically attached to the rotating shaft.
External rotor motors essentially have the opposite orientation, with the rotor rotating on the outside of the stator. This eliminates the need for an output shaft and greatly reduces the overall footprint of the motor and impeller assembly. A fan impeller can be attached directly to the external rotor, effectively creating a motorized impeller
All electric motors serve the same function of converting electrical energy into mechanical energy, but they accomplish this in different ways. The method used depends mainly on the power supplied to the motor, as this affects the way their magnetic fields are created and controlled. For this reason, motors are often categorized as being AC, DC, or EC. In the fan industry, common types of each include the AC induction motor, DC brushed motor, and EC permanent magnet motor.
AC Motor
AC induction motors have electrical windings in the stator that are supplied with alternating current to produce a rotating magnetic field. The stator field induces a current in the conductive squirrel-cage rotor, and the interaction between the two magnetic fields produces torque on the rotor. With a fixed line frequency, AC motors have a limited speed range, so they are designed to operate at the peak efficiency point on their performance curve. Outside of this range, efficiency tends to drop off significantly. A variable frequency drive (VFD) can be used to increase or decrease the frequency of the AC supply, but they tend to be quite bulky and expensive. That is why AC motors are best suited to applications where variable speed is not required.
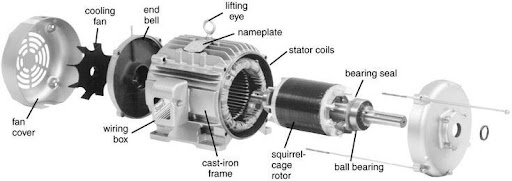
DC motor
DC brushed motors use permanent magnets in the stator to provide a fixed magnetic field. Electrical windings in the rotor are voltage induced and influenced by the stator’s magnetic field. Changing the power supply voltage allows DC motors to be speed controlled much easier than AC motors. Since they run on direct current, they rely on carbon brushes and a commutator ring to switch the current direction. Wear and tear on these mechanical components can contribute to more operational noise and a shorter life expectancy. Furthermore, DC power supplies aren’t as prevalent as they used to be, so acquiring a stand-alone AC to DC rectifier means added cost and complexity.
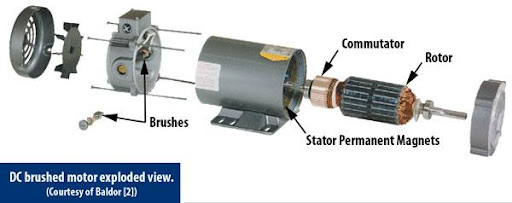
EC motor
EC motors use permanent magnets and electrical windings to generate their magnetic fields, in a similar fashion to brushed DC motors. However, as their name suggests, they achieve commutation electronically rather than mechanically. This is only possible by incorporating on-board electronics within the housing of an electronically commutated EC motor.
The on-board electronics include a rectifier that converts the AC supply to DC. An integrated controller then directs the right amount of current, in the right direction, at the right time, through each of the windings. This develops magnetic poles in the stator, which interact with the permanent magnets in the rotor.
The position of each magnet is determined by using Hall effect sensors. The appropriate magnets are attracted, in sequence, to the magnetic poles in the stator. Simultaneously, the rest of the stator windings are charged with the reverse polarity. These attraction and repulsion forces combine to achieve rotation and produce the optimal torque. Since this is all done electronically, precise motor monitoring and control are possible.
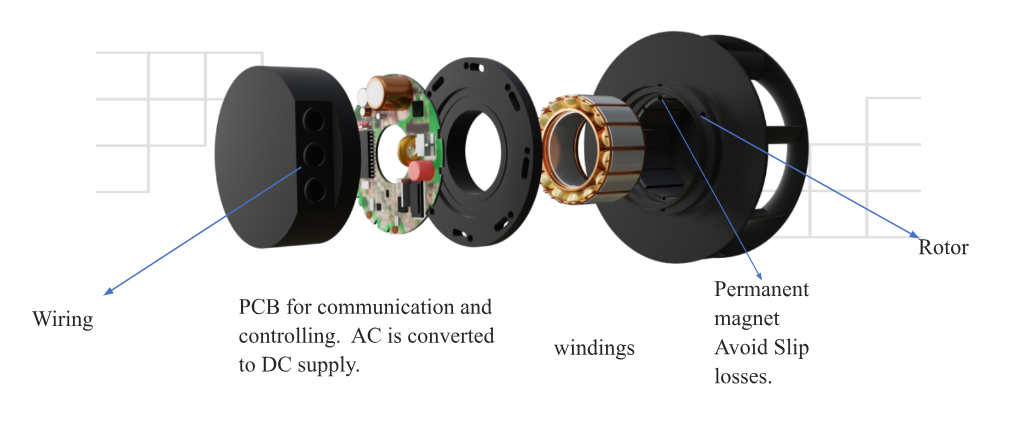
Energy Efficiency
Electronically commutated EC motor efficiency is often above 90%, allowing EC fans to consume up to 70% less energy, when compared to conventional fans.By adjusting an EC motor’s speed to match the demand, the potential for energy savings continues to grow.
While operating the EC fan we can achieve following important features- Higher Efficiency on part/Full load
- Multiple speed variation
- Zero slip loasses
- Maintenances free
Even when compared to on/off operation, the speed modulation offered by EC fans is more efficient. For example, running an EC fan 80% of the time saves 20% of the energy, while running it at 80% speed saves nearly 40-50% of the energy. This is only possible with EC technology, which offers very high efficiency across a range of speeds.
The most obvious benefit of high efficiency is lowered energy consumption. With rising energy prices, this is a crucial factor to consider.
Since EC motors produce less heat, their windings and bearings undergo less stress, which extends the life of the motor. The lower operating temperatures also contribute to higher system efficiencies, when used in cooling applications. Meanwhile, the quieter operation results in increased occupant comfort.
Ease of Control
The high efficiency of EC motors can largely be attributed to the integrated electronics. By continuously monitoring motor functions and automatically adjusting the control input, high efficiency is maintained throughout the operable speed range. EC motors are often capable of being turned down to 20% of full speed, while still maintaining 85% efficiency.
Sensors that produce a 0-10 V, PWM, or 4-20 mA signal can be connected directly to most EC motors. This provides speed control without the need for a complex variable frequency drive (VFD).Fans with electronically commutated EC motors can control temperature, pressure or whichever parameter is chosen to be measured. Constant pressure control is particularly useful for ducted applications, while constant airflow control is ideal for filtered applications.
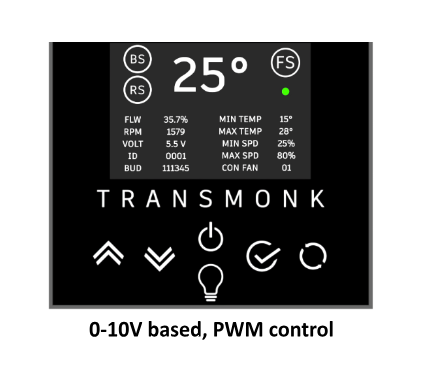
Conventional fans are controlled with a VFD, and with a VFD, we have the downside limitation of running it at 25 HZ, which indicates that we cannot ramp down the motor below 50%, and even with this 50% speed, savings are not possible. This major challenge has been resolved by EC fans. Since the internal control is PWM and it is a DC motor, we can also achieve speeds below 10% without compromising on efficiency. So running an EC fan at as low as 10% will also be possible, which will add a big benefit in terms of energy savings.
Yes, we can automate the complete fan speed from 10% to 100% based on demand-based feedback like temperature, pressure, CO2, PM 2.5, etc.
We need the required sensor and controller to be attached to it, and it will send the signal based on the set points to automate the operation. We can also automate the running hours of the EC fan.
We can use multiple EC fan grid structures to achieve higher CFM. This also gives the advantage of system redundancy, as even in the worst-case scenario, customers will have systems running with a lower CFM.
Connect with us or drop and email at northsales@transmonk.in, our engineer will connect with you.
To optimise the selection of fans, we need to know the application, the CFM, and the static required for the application.
To select the controlling system, we need to understand the basic controlling parameters of the system, such as temperature, pressure, PM, CO2, manual, etc. Once we have the data, we can provide an optimised plug-and-play solution for your product.